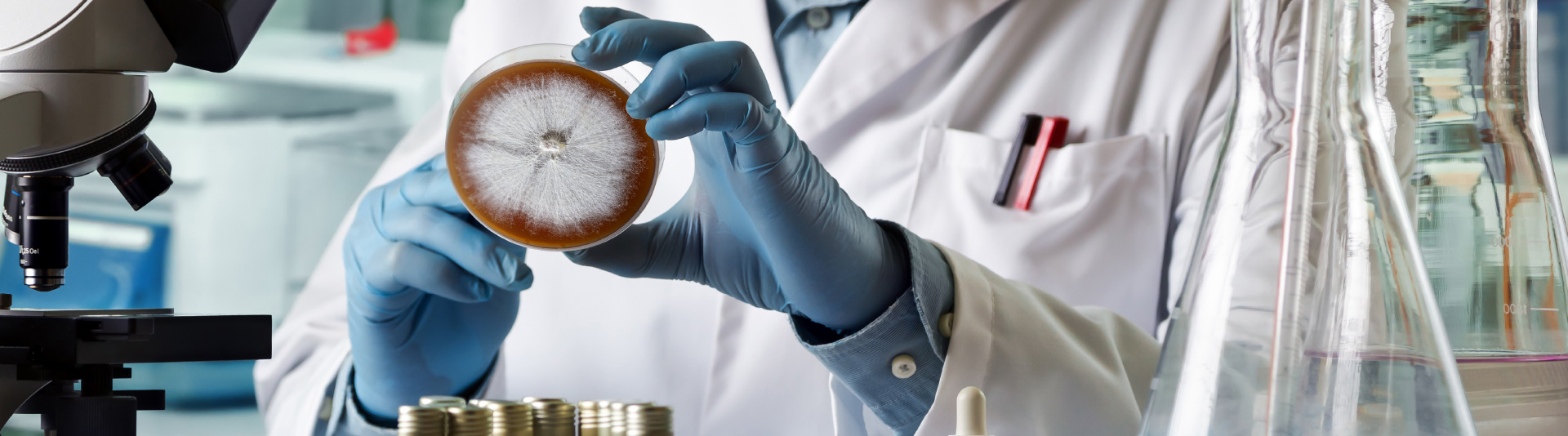
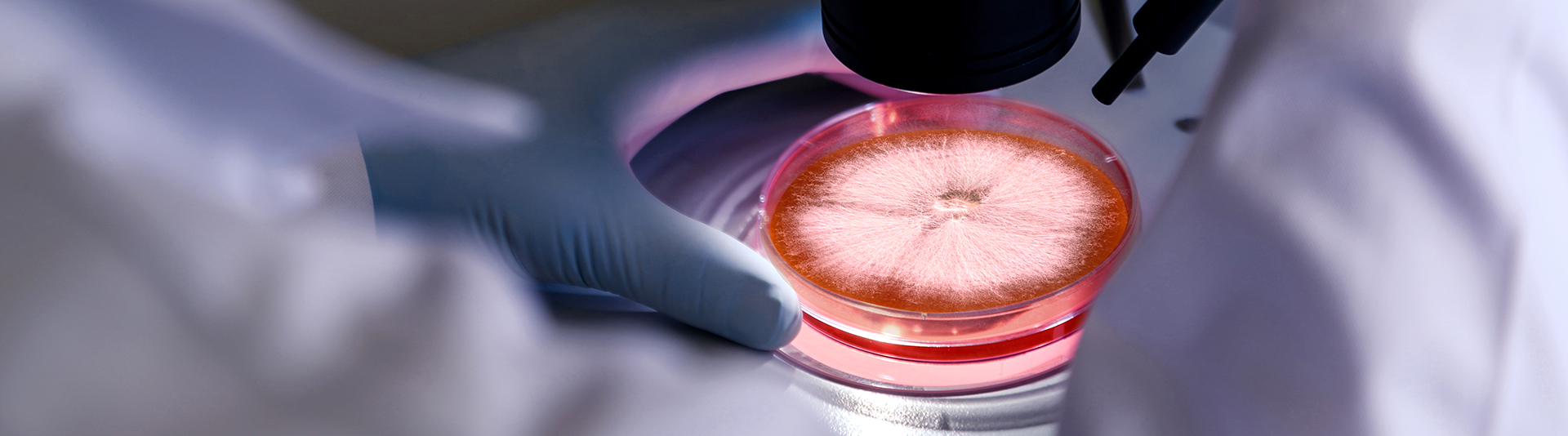
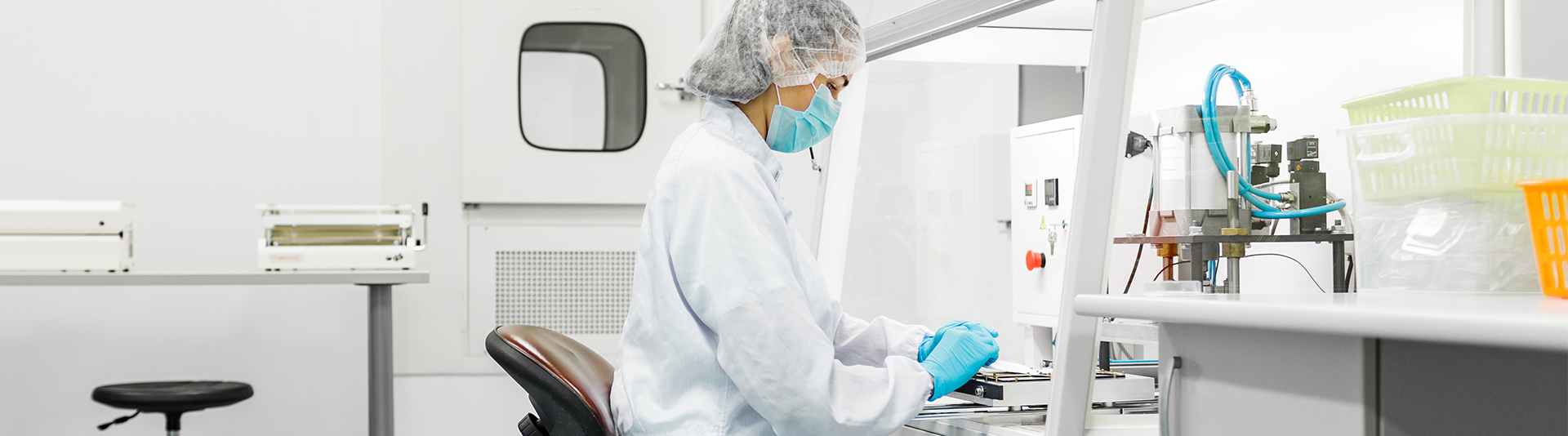
Daily program: Technology + Quality + Service
ITALSPAWN stands out for the innovative solutions of its production process, the high technology level of its research lab and the constant attention to details by the most professional staff in the industry.
All the machines involved in the production process were specifically designed and developed under the direction of the company ownership using the MOST ADVANCED EQUIPMENT on the market.
Another key element is the accurate SELECTION OF BEST PERFORMING STRAINS, in order to meet requirements such as quality, high yield and total absence of any contamination.
To maintain quality unaltered throughout the production process ITALSPAWN enforces PRECISE AND STRICT CONTROL PROTOCOLS for its cultures, which are constantly carried out by a dedicated staff.
The control of the company in the hands of the founding family represents today the best guarantee of PROFESSIONAL SERVICE and RELIABLE PRODUCTS.
Any order large or small is promptly fulfilled thanks to a FLEXIBLE PRODUCTION SYSTEM and an EFFICIENT WAREHOUSE MANAGMENT.
Point of difference
Our main goal is to maintain an excellence in the industry, recognized for quality and reliability.
And we achieve this everyday with QUALITY RAW MATERIALS, processed with advanced technologies, FLEXIBLE PRODUCTION
to suit both large or small needs and RELIABLE SERVICE AND ASSISTANCE all over the world.
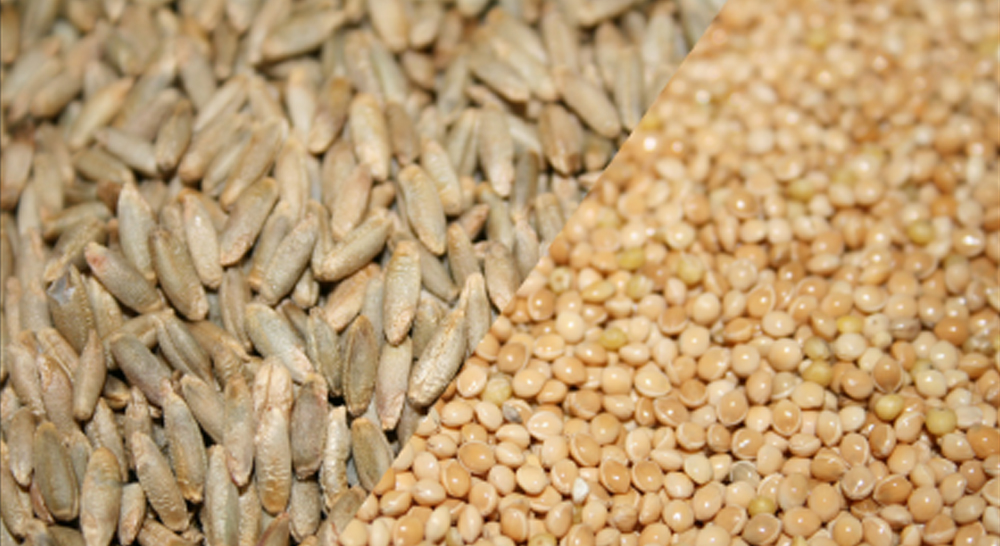
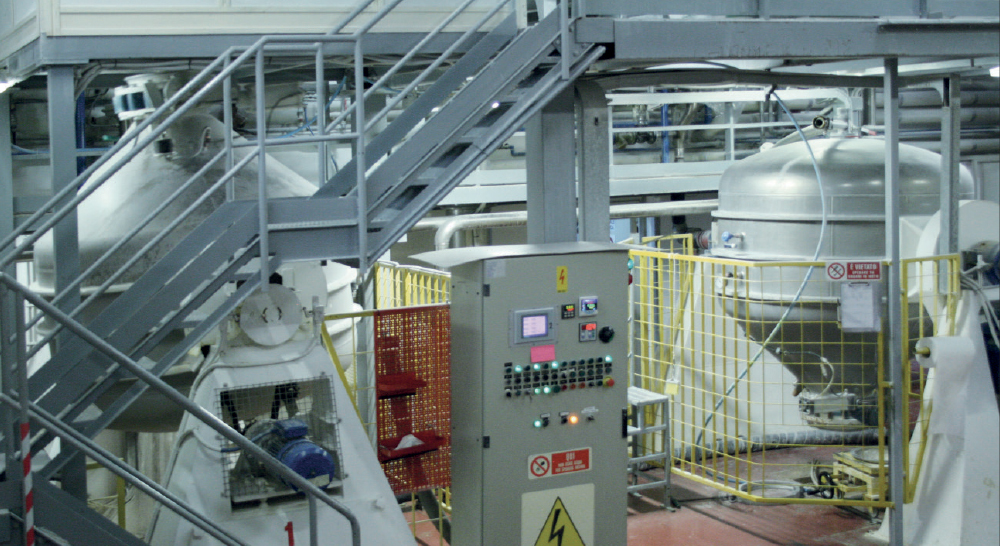
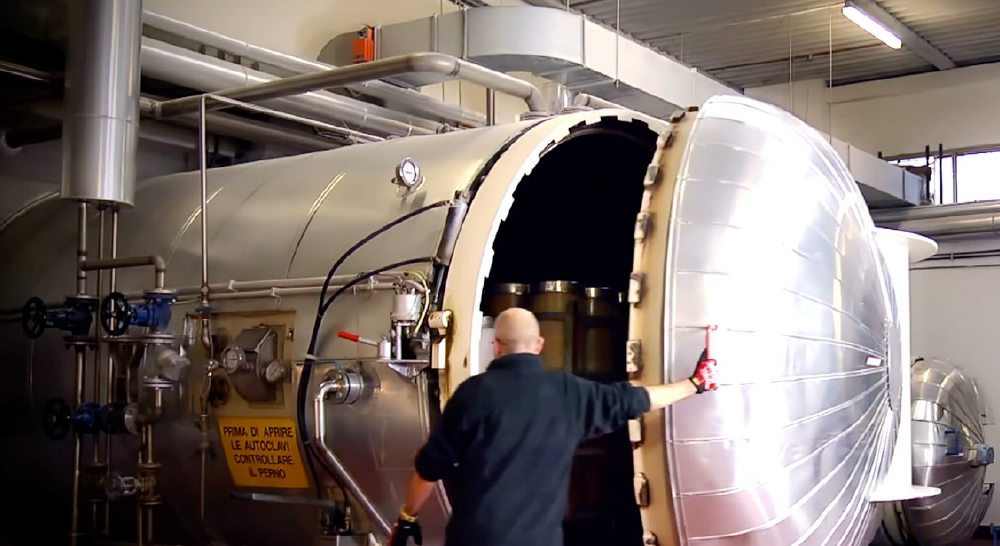
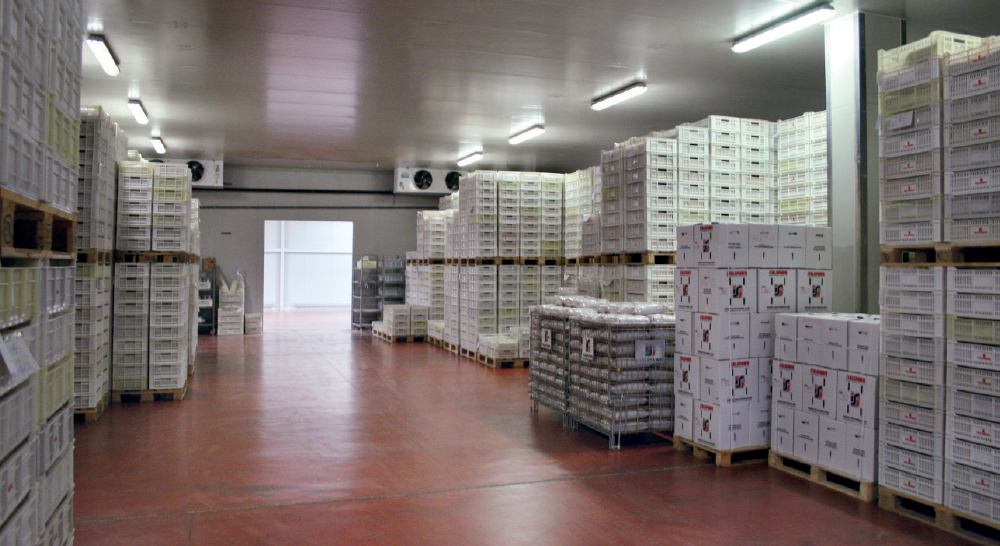
The only way to obtain the highest possible quality of a product like mushroom spawn is to use the finest quality raw materials.
This has always been ITALSPAWN production philosophy since its early days and this is why the utmost care and attention are dedicated to the SELECTION AND PREPARATION OF ITS NUTRITIVE SUBSTRATES.
All ITALSPAWN mother cultures and strains undergo a PERIODIC PROCESS OF MONITORING AND TESTING to ensure they comply with the company quality standards.
A highly qualified technical staff is employed to guarantee that the product performances respect these parameters.
In over 40 years of experience ITALSPAWN has perfected an extremely flexible and reliable production system. THE WHOLE PROCESS IS ENTIRELY COMPUTER ASSISTED in order to avoid human errors and maintain a real time control of its progress through the use of multiple monitoring devices.
Two main consecutive stages can be identified during the first phase of the process, which PREPARES THE SUBSTRATE TO RECEIVE THE SPORES THROUGH INOCULATION.
The first one is the HYDRATION OF THE PRODUCT THROUGH A COOKING PROCEDURE and the second one is the STERILIZATION WITH A PRECISE TEMPERATURE PROFILE in order to avoid any contamination and get the product ready for the next phase.
The second phase also includes two different stages. The first one is the INOCULATION AND BAGGING PROCEDURE which takes place in a totally sterile air filtered environment where the grain is mixed with sterile inoculum and packed inside sterile filtered bags. The second one is a MULTI STAGE COOLING DOWN INCUBATION to let the spawn mature and get ready for final storage.
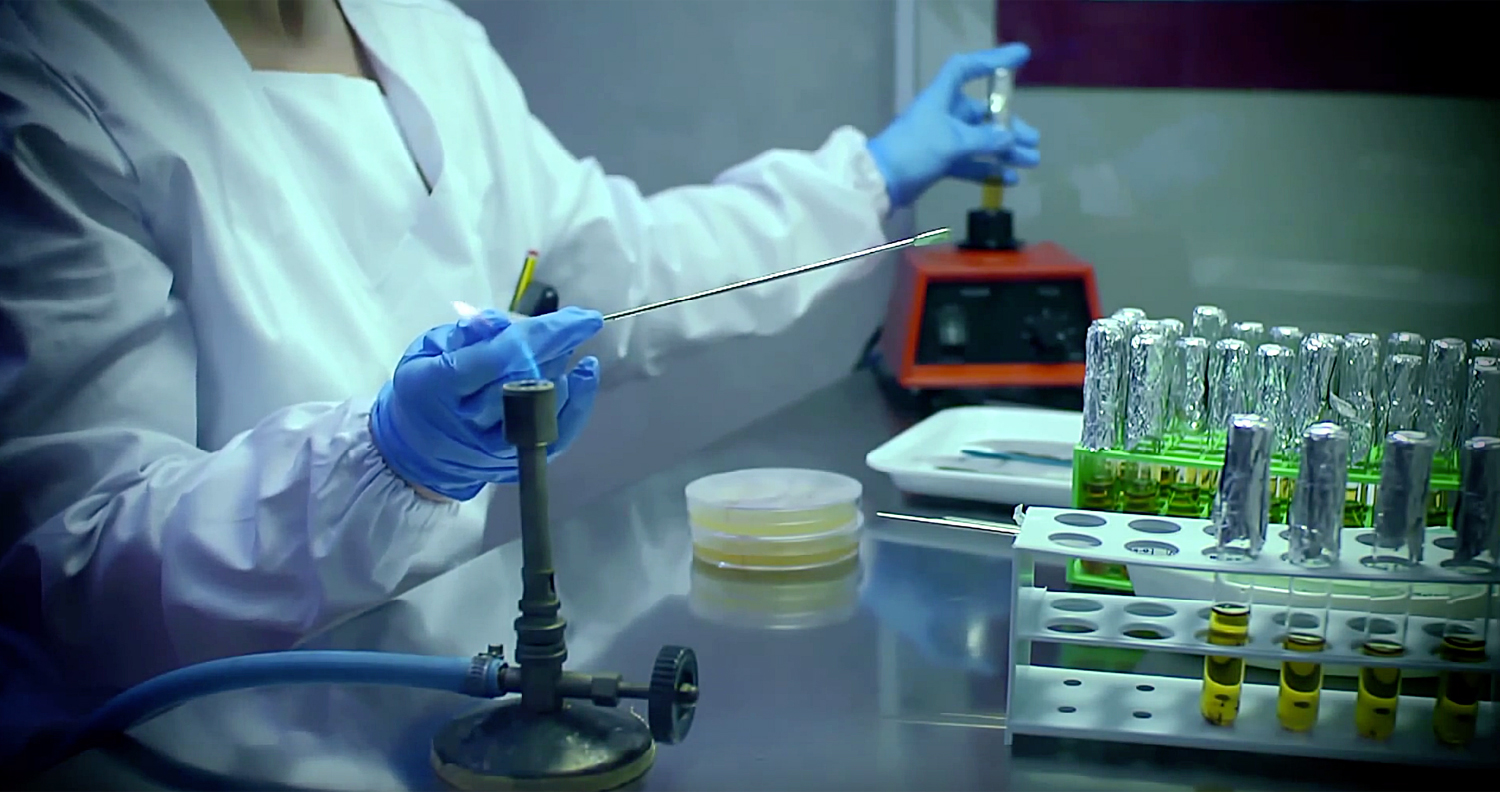
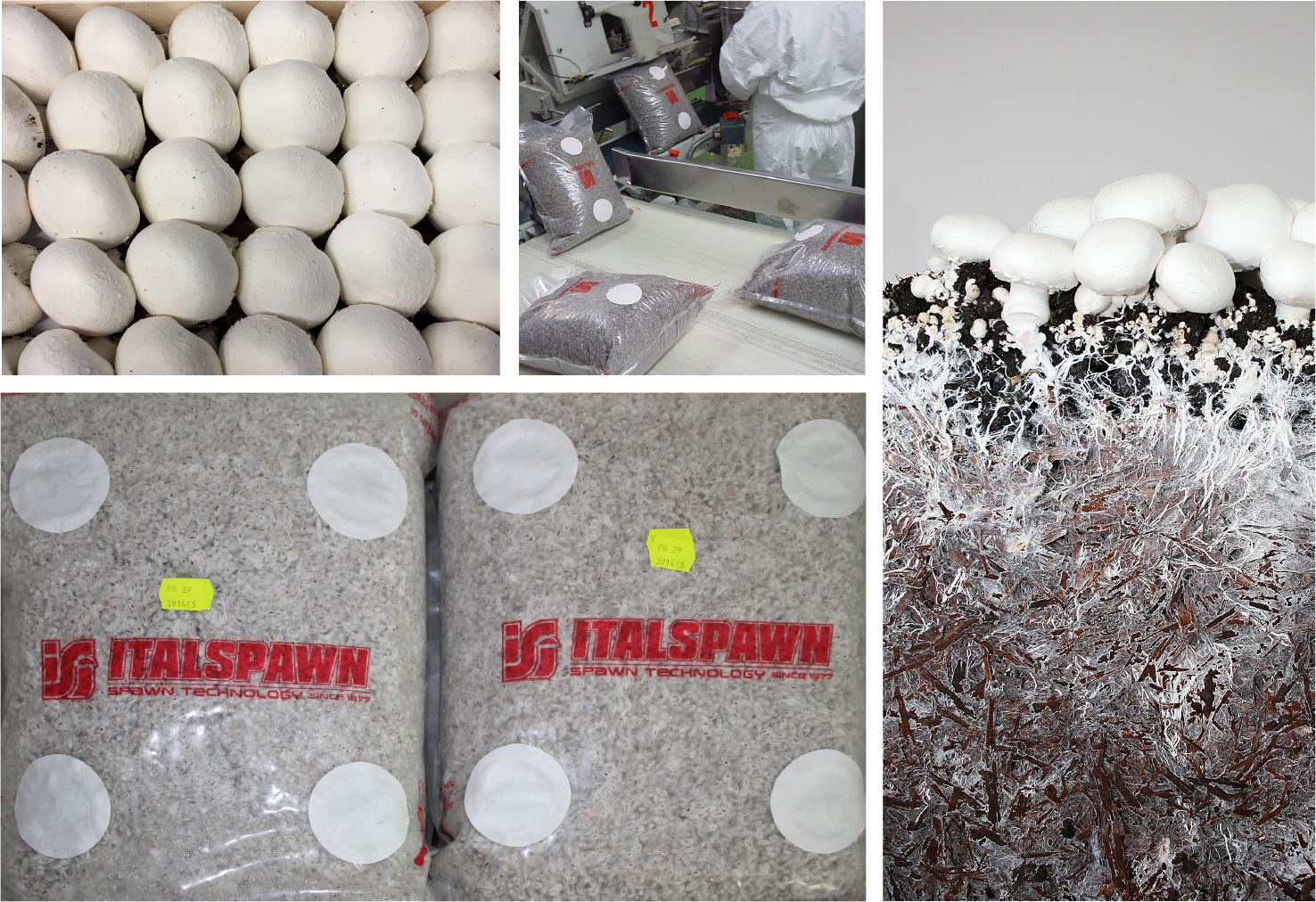